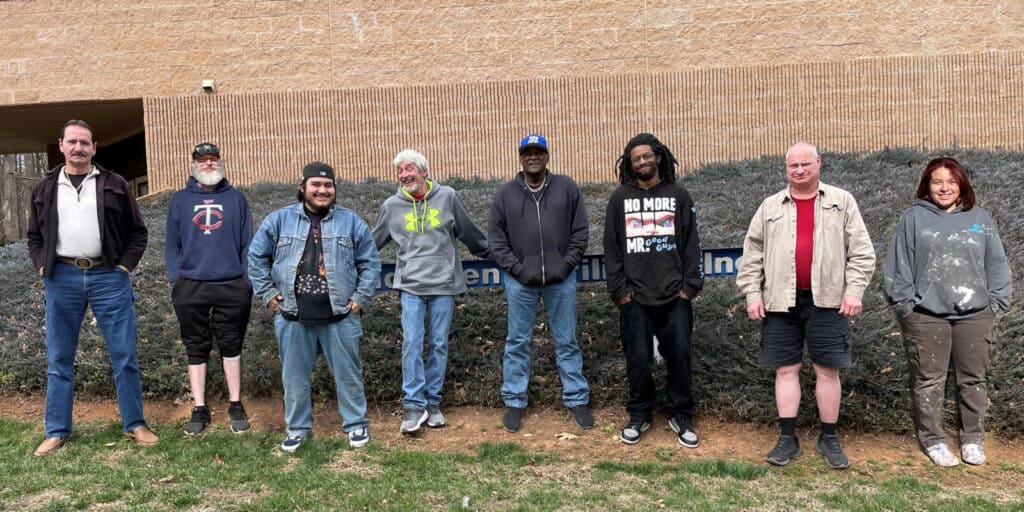
These days, it seems nearly everyone lays claim to the personality trait “detail-oriented.”
Andersen’s Hardware Department, however, embodies that trait and elevates it to something truly meaningful.
Hardware Department: Mike Koschmider, Auman Hunter, Miguel Mendoza Garcia, Henry Dougherty, Bernard Wall, Mike Mitchell, Todd Sharpe, and Isabel Esparza
Most know that Hardware manufactures Andersen’s sterilizers. But many do not know that the department tracks the journey of every single screw from receiving to shipping it out as part of a sterilizer.
The process (in a nutshell): Raw parts are moved from upstairs to down; sub-assemblies are made; a pick list is issued that details every single part needed to build however many sterilizers are being built at once (often five Anprolenes and single EOGas model); parts are “picked” and placed in a blue bin; blue bin contents reviewed by a supervisor; machine(s) assembled and run overnight and, finally, quality tested. Quality testing ensures all parameters are in good order including the cosmetics, functionality, paperwork and lot numbers.
Post-assembly, each sterilizer runs the gauntlet of around 23 forms (depending on the model). These forms are a last check all the labels are affixed, everything is included on and in the sterilizer that should be, it can withstand a surge, its feet are level and so much more. In this process, 41 images are taken of each sterilizer. The image list has been generated over the years based on customer feedback. The Quality Assurance (QA) department reviews every image to ensure we avoid common manufacturing errors.
Hardware uses Global Shop for ordering, receiving, tracking parts and shipping sterilizers. The intricate, Tetris-like dance of securing parts, pulling them together into secondary parts (sub-assemblies) and then finally into the finished sterilizer – in timed synchronization with customer needs – would not be for the faint of heart or scattered of mind.
Luckily, Hardware has at the helm Henry Dougherty, with more than twenty years’ experience. In New Jersey, where he grew up, Henry attended a vocational and technical high school. He got an early work release to build sound-proof cabinets for a company that produced loud machines. Henry soon ended up building more cabinets than there were machines to put in them and the company offered him a job on the manufacturing floor. Within 6 years he was running the manufacturing floor.
The company moved to North Carolina in 1997 and Henry came with it. Ethan Marshall worked at the same company. When it moved manufacturing overseas, Ethan suggested Henry consider working at Andersen.
Henry came to work at Andersen in 2019 building EOGas 333 – the large refrigerator-sized models. But a few years later the Hardware supervisor left and he took over the role.
“When people ask me why I drive over an hour from Cary each day to work at Andersen,” said Henry, “I say ‘I like what I do, I like the people I work with, I’m good at what I do and I love working with Ethan as my direct supervisor.’”
Henry is proud of his team and the environment he provides for them. Hardware has become something of a safe harbor for many who did not feel at home in their first position at Andersen. Far from finding the rigorous attention to detail difficult, those who have found a home in Hardware see the highly structured environment with explicit expectations as a refuge. “The pleasure of working with your hands and seeing progress at the end of the day,” he explained, “tends to lead to job satisfaction.”
Every task in Hardware has extensive Standard Operation Procedures (SOPs) outlining each step with images.
“Up here we converse every day,” said Henry, “who needs help, who can give help to someone else. We have each other’s back. We’re cross-trained so everyone gets the time off they deserve.”
When asked about future goals, Henry said he would really like to “force feed Products.” In other words, he would like to be enough ahead of schedule, there is always an inventory of finished cabinets. “That way the customer never has to wait.”
So, all of these details? They add up to the same thing: Serving the customer. Making sure their sterilizer is masterfully built, safe to operate and delivered on time. And that is, truly, meaningful.