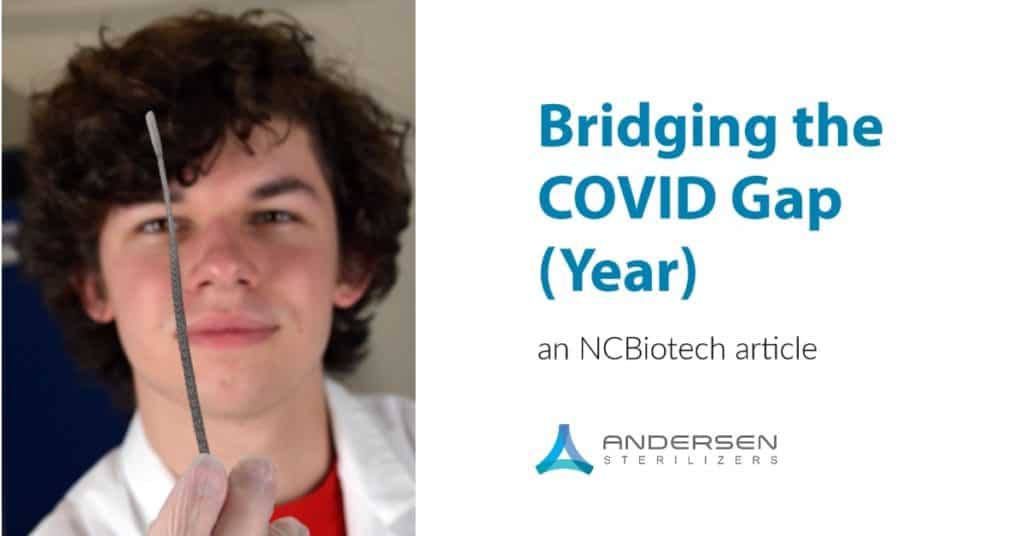
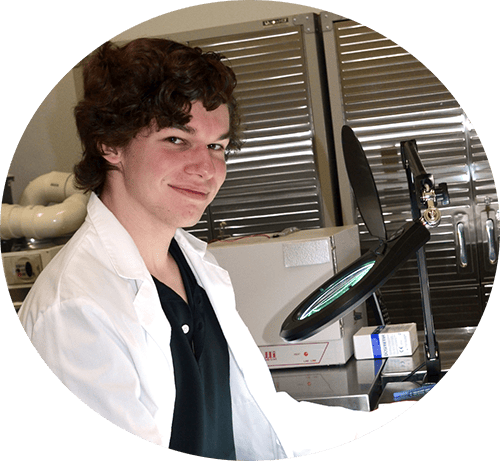
In the spring of 2020, Carl May was graduating high school and preparing to enter college in the fall. However, 2020 was unlike most years; the COVID-19 pandemic was underway and ramping up.
Carl is the grandson of Andersen Sterilizer’s founder Dr. H.W. Andersen. He belongs to a family with deep roots in the healthcare industry. When the opportunity arose to work at Andersen Scientific, a contract sterilization sister company to Andersen Sterilizers, Carl chose that option over distance learning. He requested a deferment from college to spend the year doing his part in the fight against the virus.
Carl trained at the Andersen Scientific laboratory in Morrisville, NC, as a sterile processing technician. He was soon tasked with the preparation and processing of millions of COVID test swabs.
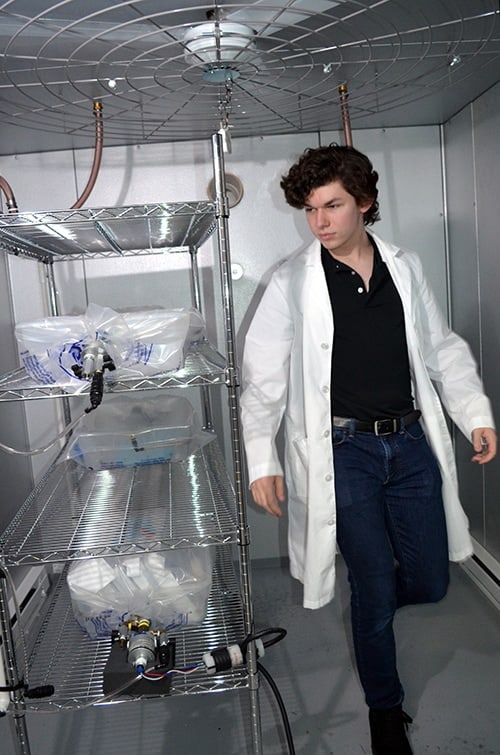
The Andersen facility uses an exclusive ethylene oxide sterilization method, recently recognized in a FDA Innovation Challenge. In his time at Andersen Scientific, Carl learned to seal product into EO-impermeable bags with a gas cartridge and other consumables, and then load the bags into temperature-controlled sterilization cabinets. After an overnight exposure cycle, followed by an EO purge and aeration cycle, the swabs were sterilized and ready to be shipped. They were typically sending out product the day after they received it.
“The swab manufacturers were under great pressure, and they frequently could not give us advance notice of shipments,” Carl said. “Pallet loads of swabs would show up in the afternoon and would need to go into the sterilizer that night.”
Surprise deliveries and rush orders resulted in many workdays where his shift extended into the night. Despite the long hours, Carl said he was inspired by a sense of mission and the importance of the work.
“Our processing protocols are very detailed. Mistakes could require that a load be entirely reprocessed. The time urgency of these shipments can make the work difficult. However, it was great knowing that the swabs were badly needed by hospitals around the country.”
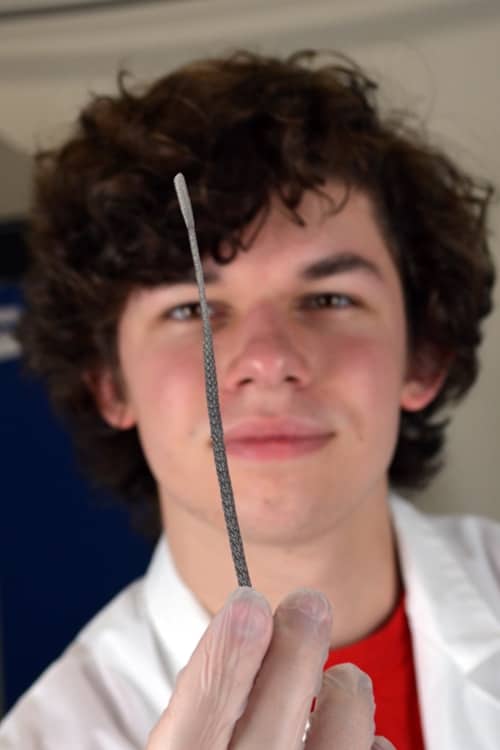
Each pallet of COVID test swabs represented over 28,000 swabs. At the peak of the pandemic, Andersen Scientific was sterilizing swabs for four companies – frequently three pallets a week, and at times as much as a pallet per day. That’s swabs for hundreds of thousands of COVID tests being distributed across the country every week.
Swabs can be very simple devices. However, the crisis gave rise to innovative new designs. “One company developed a new 3D swab. It was pretty exciting to help bring this new product to market.”
When asked why a company like Keystone Solutions Group, the largest of the swab manufactures, may choose to work with Andersen Scientific, Carl said, “I believe our turnaround time, level of customer service, depth of sterilization knowledge and price are hard to find elsewhere. We put a lot of care into what we do, and we work hard to cater to every client’s individual needs. For small and medium sized producers, Andersen Scientific provides benefits you just won’t find at large contract sterilization plants.”
With US universities returning to in-person learning, Carl is looking forward to starting his freshman year in college in August 2021.
“I learned a lot this year. My previous science classes have all been theoretical. It was really interesting to learn the science behind the sterile processing of swabs and gain hands-on experience during this critical time for the world.”