Bryant Haskins, NCBiotech writer – reproduced from original article with permission
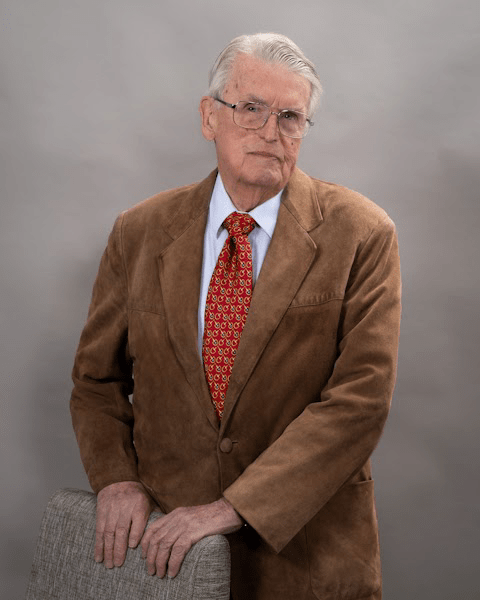
When Dr. Harold Andersen was a young surgical resident in New York City, he saw two patients die after gastric drainage tubes failed to work effectively during their surgeries.
So he and his father, an engineer, designed a better nasogastric tube in the family’s basement. It was such an improvement over other devices that the renowned Bellevue Hospital ordered 5,000 of them and Andersen Products was born. It was 1958.
The need to sterilize the tubes for medical use soon led to a second innovation, a new type of ethylene oxide (EO) gas sterilizer. Designed by Dr. Andersen and a childhood friend – also an engineer – it was the genesis of Andersen Sterilizers. In the years since, the company has evolved into a thriving family-owned medical device manufacturer headquartered in the Health Science Park in the small Alamance County town of Haw River.
Andersen makes different sizes of sterilizers under the Anprolene and EOGas labels. It sells the products to some 6,000 customers in the U.S. and more than 50 other countries. Clients include hospitals, day surgery centers, veterinary clinics, research and clinical laboratories, and medical device manufacturers.
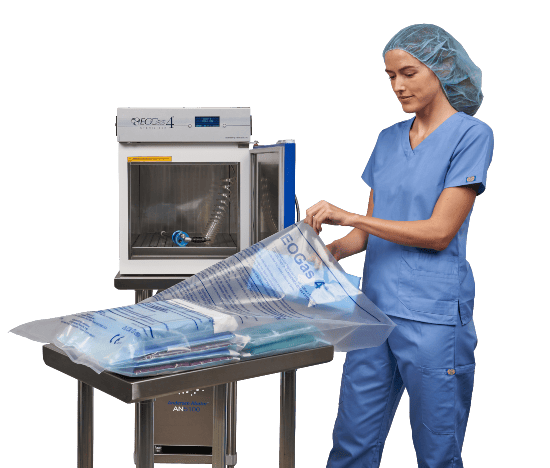
Last year the company also opened a new Andersen Scientific facility in Research Triangle Park (RTP). Andersen Scientific provides rapid turn-around contract sterilization services, primarily to small and medium-sized companies and research organizations that don’t own and operate their own sterilization equipment.
The business has become a particularly valuable resource during the COVID-19 pandemic. Manufacturers of COVID testing swabs rely on Andersen to sterilize those products before use, to prevent false readings.
The company currently employs 120 people in North Carolina – 150 worldwide – and contracts with about 50 North Carolina-based suppliers to provide the raw materials it needs to operate, according to CEO Ted May. All Andersen sterilizers are manufactured in North Carolina.
Dr. Andersen, now 89, remains chairman of the company. “He still comes to work every day,” said May. “His first love is developing new products and he spends a lot of time with our engineers.” Dr. Andersen’s son Bill, an orthopedic surgeon and engineer with a sports medicine practice in nearby Cary, also is involved in the business as president of manufacturing.
Flexibility and a focus on customers and the environment
What sets Andersen apart from its competitors – primarily large contract sterilization companies – is its flexibility, focus on smaller businesses, and an enviable environmental footprint, according to May.
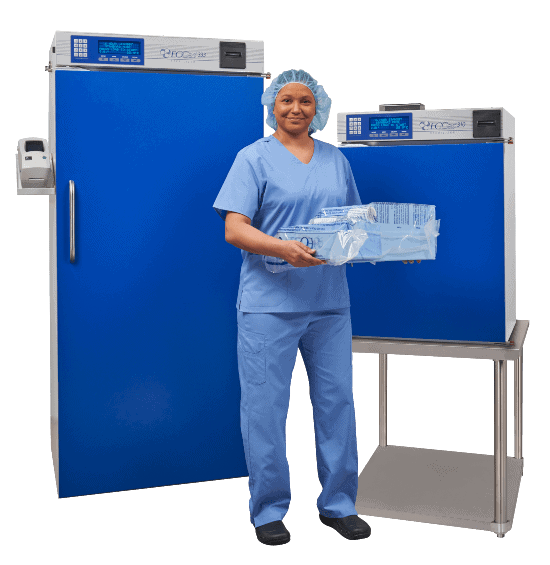
Most of the big contractors rely on large sterilization chambers that can use hundreds of pounds of ethylene oxide to sterilize truckload-sized pallets of products, he explained. Andersen sterilizers range from tabletop models to units that are about the size of refrigerators. They’re designed to meet the specific needs of clients that range in size from small research labs and veterinary clinics to full-blown medical device manufacturers.
Andersen products use individual vacuum-packed bags with sterilization cartridges that require only a small amount of ethylene oxide. The bags collapse around the products, eliminating any dead space so that a high gas concentration is achieved with just a little EO.
Depending on the size of the Andersen sterilization unit, it can handle anywhere from one to 10 bags of products at a time, May said. As businesses need more volume, they can increase the number of sterilizers they use. Andersen Scientific’s contract sterilization models can process up to 50 bags per run.
Extremely low ethylene oxide emissions
Ethylene oxide, in large amounts, can cause safety and environmental concerns. While EO is one of the most effective ways to sterilize medical and related equipment – an estimated 50% of new medical supplies are handled this way – the gas is flammable. And exposure can cause potential health problems. So the EPA tightly regulates EO emissions.
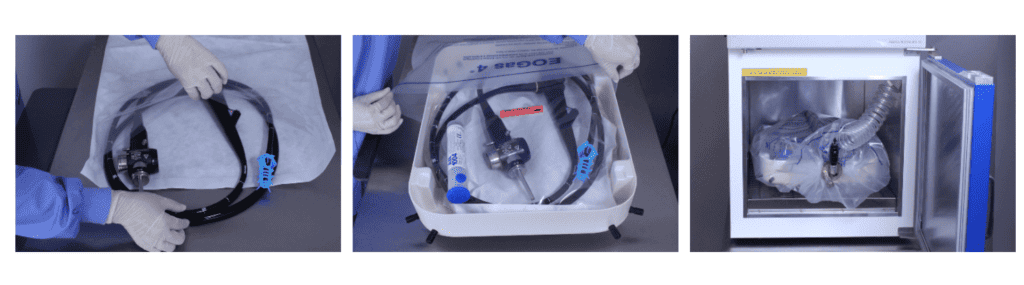
May said Andersen’s sterilization systems use only 17.6 grams of EO per cycle – 90 percent less than any other units on the market.
Specially designed ethylene oxide abatement systems can be added to the sterilizers to reduce emissions to almost zero, he added. With those systems, the sterilizers emit less than a pound of EO a year.
That’s in stark contrast to the hundreds, and sometimes thousands of pounds of EO gas released annually from large sterilization chambers.
The National Steering Committee of the Small Business Environmental Assistance Programs and Small Business Ombudsmen recently singled out Andersen for a 2020 Environmental Stewardship Award in recognition of its high-efficiency, low-emission sterilization equipment.
And this past November, Andersen became the first medical sterilization manufacturer to receive U.S. Food and Drug Administration 510 (k) clearance to use its EOGas 4 sterilization system for duodenoscopes and colonoscopes. These reusable surgical devices have been linked to dangerous and sometimes fatal infections.
Providing an advantage to North Carolina businesses
While Andersen’s market is global – 40% of its products are sold to companies outside the U.S. – it’s a particularly valuable resource to North Carolina’s fast-growing research, pharmaceutical and biotechnology sectors. In fact, business leaders in the state persuaded Dr. Andersen to relocate his Oyster Bay, New York company more than three decades ago – in 1985 – because they realized the importance of sterilization services to companies in an expanding North Carolina life sciences ecosystem.
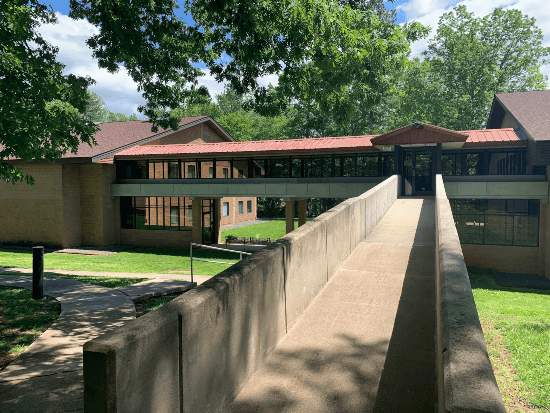
Dr. Andersen put down roots on what is now an eight-building, 50-acre campus in Haw River. The company headquarters – just a few minutes’ drive from the Research Triangle – houses manufacturing, quality assurance, R&D, distribution, and sales and marketing. Andersen owns another 50 acres of adjoining property, so it has plenty of room to grow. It currently has about 150 customers in North Carolina.
Andersen Scientific is likewise strategically located in the heart of RTP.
“We’re proud to work with a wide range of innovative medical device and biotech startups here in the greater RTP region,” May noted. “The fact that we’re close to our North Carolina customers is a real plus because sterilization services, shipping and the supply chain have become increasingly difficult for small and medium-sized businesses to navigate. We can provide the services they need, often on a 24- to 48-hour turnaround.”
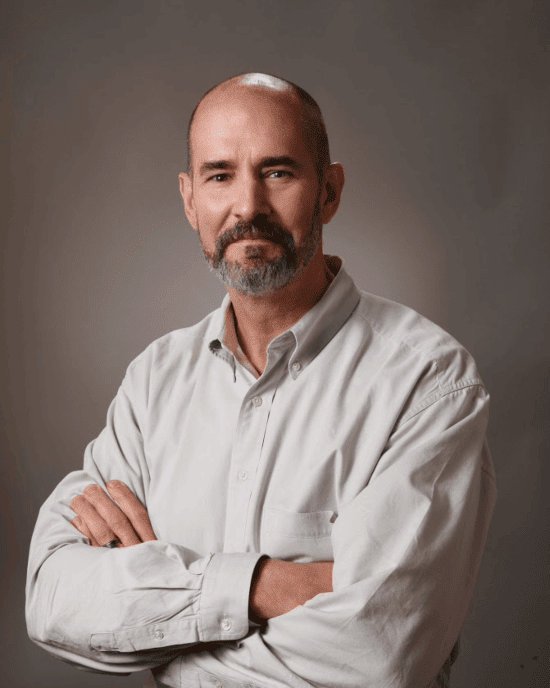
Non-medical applications
In addition to its customary clients, Andersen has been called upon to sterilize products that aren’t at all medically related:
- The company has sterilized swabs for DNA testing labs so criminal evidence isn’t vulnerable to cross-contamination. And England’s Scotland Yard and other law-enforcement agencies depend on Andersen equipment to sterilize all their evidence-gathering paraphernalia.
- The company is working with researchers in different parts of the country who are trying to identify the causes of colony collapse disorder – a phenomenon that occurs when most of the worker bees in a honeybee colony disappear. Andersen’s gas sterilizers are so gentle that they can be used to remove all microbes from the pollen that bees feed on.
- And federal government agencies used Andersen sterilizers on incoming mail during the anthrax assaults of 2001, which followed close on the heels of the September 11 terrorist attacks on the World Trade Center and Pentagon.
Helping customers perform miracles
But medically related businesses are the company’s primary focus. May said one of Andersen’s biggest strengths is its commitment to those clients. “Our mission statement is ‘Helping our customers perform miracles,’” he added. “They include world-class clinicians, scientists, biotech engineers and researchers. We’re proud to play a small part in their efforts to change the world.”
For more on Andersen, please take an amazing tour “Beyond the Tour” by clicking on this video. And this video testimonial from an NC-based plastic surgeon. There’s also this informative 4-minute “How-to” video demonstrating the loading and operation of Andersen’s Anprolene sterilizer system.